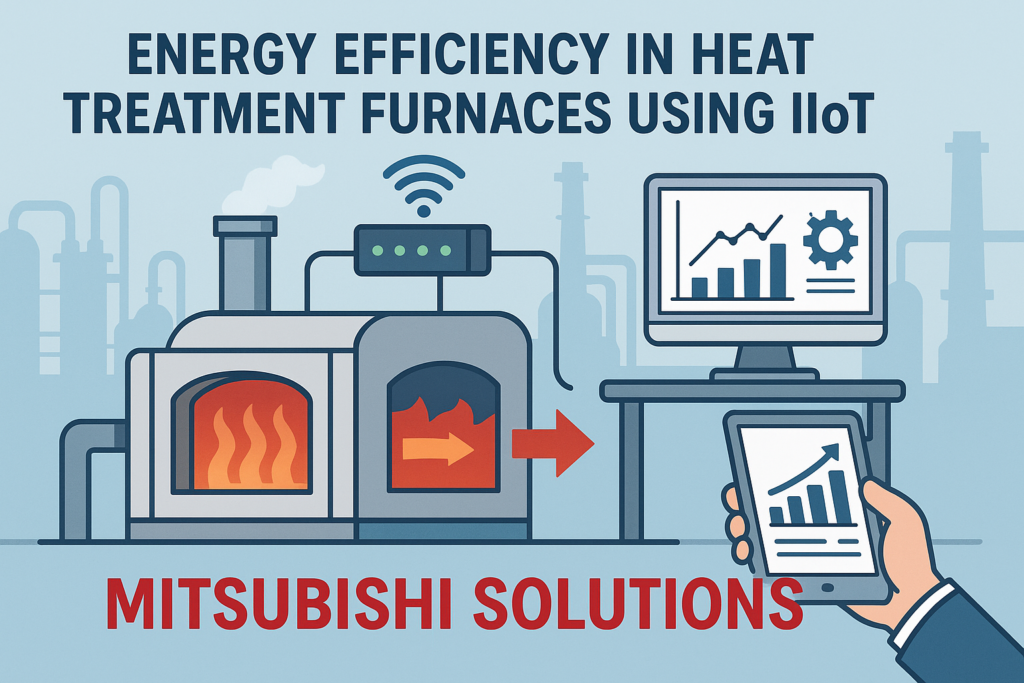
The heat treatment process plays a critical role in the manufacturing of metal components, shaping the mechanical properties of the material, such as hardness, ductility, and tensile strength. However, heat treatment furnaces are typically high-energy-consuming equipment, and their operation often accounts for a significant portion of energy costs in industries such as automotive, aerospace, and manufacturing. The need for reducing energy consumption while maintaining precise control over the furnace temperature has never been more critical.
In recent years, Industrial Internet of Things (IIoT) technology has emerged as a game changer in furnace management, offering solutions for enhanced energy efficiency. Mitsubishi, a leader in industrial automation, has pioneered IIoT-driven systems that provide real-time monitoring, analytics, and control, enabling manufacturers to reduce energy consumption during heating and cooling cycles.
Techniques for Reducing Energy Consumption in Heat Treatment Furnaces
Energy efficiency in heat treatment furnaces can be approached from multiple angles, ranging from process optimization to system integration. Mitsubishi’s IIoT solutions offer advanced tools to enhance every stage of the heating process.
1. Optimized Heating and Cooling Cycles
The heat treatment process involves precise temperature control during both heating and cooling stages. Traditionally, controlling these cycles requires significant energy input to maintain the correct temperature range for the required amount of time. However, with IIoT technologies, heat treatment furnaces can be equipped with sensors and smart controllers that monitor the furnace’s internal conditions in real time.
Mitsubishi’s MELSEC iQ-R Series and E-F@ctory solutions integrate sensors, PLCs (Programmable Logic Controllers), and cloud-based platforms to collect real-time data, such as temperature readings, energy consumption, and furnace operation times. By analyzing this data, IIoT systems can optimize heating and cooling cycles by adjusting energy inputs based on the real-time needs of the furnace.
For instance, if the furnace reaches the desired temperature earlier than anticipated, the system can adjust the heating rate, thereby avoiding unnecessary energy consumption. Similarly, during the cooling phase, the system can regulate the cooling time based on the specific material and desired properties, ensuring the furnace does not consume excessive energy.
2. Load Optimization
IIoT systems can also optimize energy consumption by dynamically adjusting furnace operations based on the load being processed. Different loads may require different heating profiles. For example, a smaller batch may reach the desired temperature faster than a larger batch, allowing the system to adjust its energy usage accordingly.
Mitsubishi’s MELSEC-Q Series can detect variations in load and adjust furnace behavior without manual intervention. This process not only reduces energy usage but also improves the consistency and quality of the heat treatment process, which is vital for industries with stringent standards.
3. Adaptive Control Based on Data Insights
One of the standout features of IIoT systems is the ability to continuously learn and adapt based on the data they collect. Mitsubishi’s IIoT solutions enable predictive maintenance, where sensors monitor key components such as burners, heating elements, and temperature sensors. If a component is operating inefficiently, the system can automatically adjust furnace parameters or even schedule maintenance to avoid energy wastage.
By analyzing historical energy consumption patterns, IIoT systems can predict optimal energy usage based on the furnace’s specific needs, ensuring the furnace runs at peak efficiency without overconsumption.
The Role of Furnace Insulation in Energy Efficiency
Insulation is one of the most straightforward and cost-effective ways to reduce energy consumption in a heat treatment furnace. The temperature inside a furnace can reach extreme levels, and without proper insulation, much of the heat generated is lost to the environment, which forces the system to work harder to maintain the desired temperature.
Mitsubishi’s IIoT solutions can help track furnace temperature fluctuations and alert operators when heat loss exceeds acceptable levels. This enables timely inspections of the insulation and other heat-retaining components. Monitoring can also help identify areas where insulation may need to be upgraded or replaced, which further improves energy retention and efficiency.
Advanced Materials for Furnace Insulation
In addition to IIoT-driven monitoring, advancements in materials used for furnace insulation play a significant role in reducing energy loss. High-quality refractory materials and advanced thermal coatings can reduce heat loss, ensuring that the energy used to heat the furnace stays within the system longer. Mitsubishi’s technology can integrate real-time data with predictive algorithms to assess whether new insulation materials or coatings are required based on performance trends over time.
Energy Recovery Systems
Energy recovery systems play a key role in enhancing the energy efficiency of heat treatment furnaces by capturing and reusing waste heat. In a traditional furnace, much of the heat is lost through exhaust gases, but with Mitsubishi’s advanced IIoT solutions, heat recovery systems can be integrated seamlessly to capture and reuse this energy.
For example, Mitsubishi’s E-F@ctory platform can link the heat treatment furnace to a system that captures exhaust gases and recycles the energy to preheat the incoming air or water used in the heating process. This reduces the need for additional energy sources, cutting down on the overall energy requirements of the system.
In addition to waste heat recovery, Mitsubishi’s system can monitor the temperature of exhaust gases and ensure that the energy recovery system is functioning optimally. If the system detects a drop in the recovery efficiency, it can trigger maintenance alerts, allowing for timely interventions before energy wastage becomes a significant issue.
Conclusion
As the demand for energy efficiency increases, Mitsubishi’s IIoT solutions offer a powerful toolset for reducing energy consumption in heat treatment furnaces. By leveraging real-time data, advanced control systems, and energy recovery technologies, manufacturers can optimize heating and cooling cycles, enhance furnace insulation, and ensure more effective use of waste heat. The result is a more energy-efficient, cost-effective, and environmentally friendly heat treatment process that not only improves the bottom line but also helps companies meet sustainability goals.
With Mitsubishi’s IIoT-driven solutions, industries can embrace smarter, more efficient furnace operations that deliver both economic and environmental benefits—creating a sustainable future for heat treatment technology.
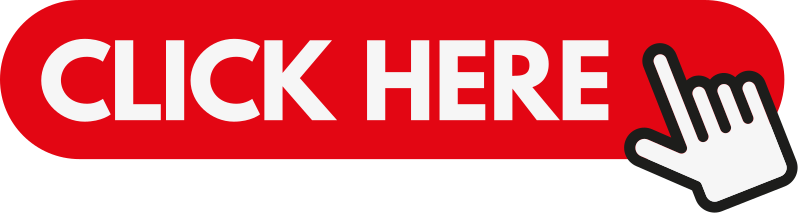
Leave a Reply